In horizontal pipes, the flow patterns of gas and liquid exhibit variations, typically classified into different regimes based on flow characteristics.
Here’s an overview of the primary gas/liquid flow patterns in horizontal pipes:
– Stratified Flow:
This pattern involves the separation of gas and liquid phases into distinct layers. The liquid forms the bottom layer, while the gas occupies the upper layer.
– Annular Flow:
Characterized by a thin film of liquid flowing along the pipe walls, with the gas phase flowing in the central core.
– Slug Flow:
In slug flow, large gas bubbles are separated by liquid slugs. The liquid slugs move along the pipe, and the gas bubbles can be intermittent or continuous.
– Bubble Flow:
Small gas bubbles are dispersed throughout the liquid phase, creating a bubbly appearance. This pattern is often associated with lower liquid flow rates.
– Plug Flow:
Consists of alternating sections of liquid and gas plugs, sequentially moving through the pipe.
– Spray Flow:
Involves the dispersion of liquid droplets in the gas phase, commonly occurring at higher gas velocities.
– Wavy Flow:
Characterized by waves or undulations on the interface between the gas and liquid phases. The waves can vary in amplitude and wavelength.
Transitions between these flow patterns can be influenced by factors such as flow rates, pipe diameter, fluid properties, and pipe inclinations. Understanding these patterns is crucial in various industrial processes, including oil and gas transportation, chemical processing, and heat exchanger design, impacting the efficiency and performance of these systems. Flow pattern maps are often used to visualize different regimes under varying operating conditions.
In conclusion, a comprehensive understanding of gas/liquid flow patterns in horizontal pipes is essential for optimizing industrial processes. By delving into these patterns, engineers can enhance the efficiency and reliability of systems involved in oil and gas transportation, chemical processing, and heat exchange.
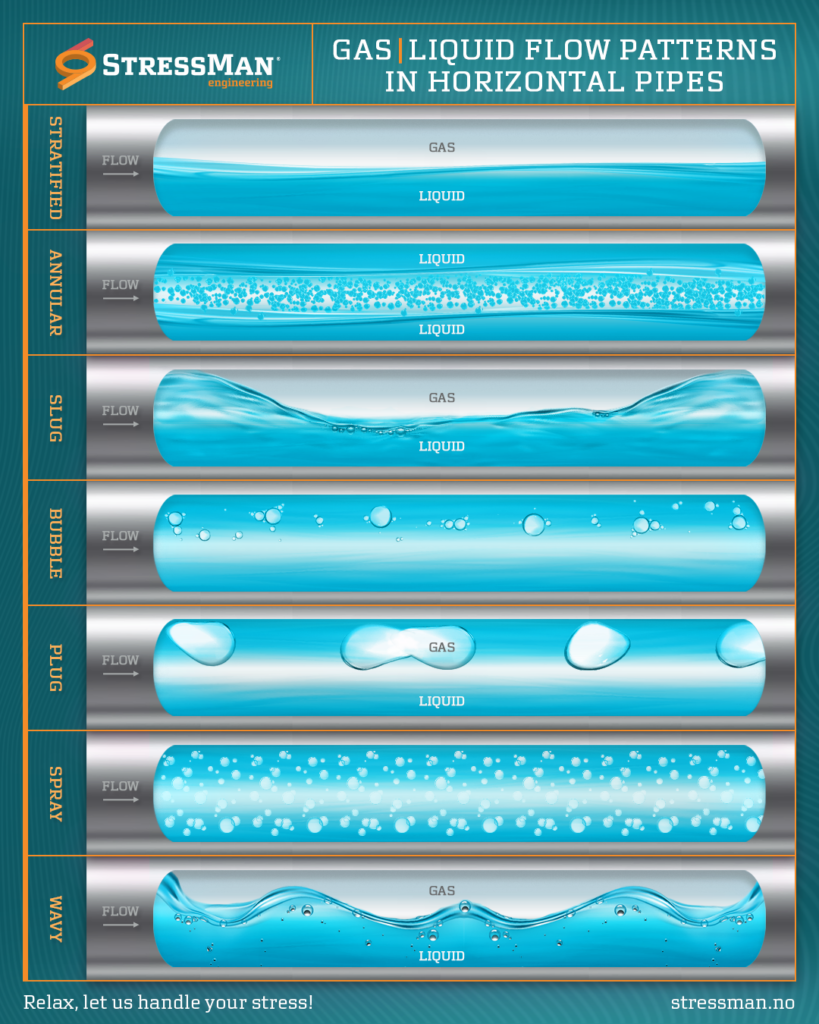