Introduction:
Heat exchangers are fundamental devices in various industries, facilitating efficient heat transfer between fluids. Choosing the right Tubular Exchanger Manufacturers Association (TEMA) type and optimizing the thermal design of a shell and tube heat exchanger are critical steps to ensure their effectiveness while keeping costs in check. This comprehensive process involves a series of steps, each playing a pivotal role in achieving the desired performance. Let’s explore these steps in detail:
Key Steps in Shell and Tube Heat Exchanger Design:
1. Understand the Application Requirements:
Before diving into the design, it’s essential to comprehend the specific needs of the heat exchanger’s intended application. Factors like heat load, temperature ranges, fluid properties, and unique considerations must be thoroughly assessed.
2. Select the TEMA Type:
Choosing the appropriate TEMA type is a foundational decision. TEMA provides standards and guidelines tailored to different heat exchanger applications. Selecting the right type ensures compatibility with the process requirements.
3. Determine Design Parameters:
This step involves defining critical design parameters, including tube diameter, tube length, shell diameter, and tube layout. These parameters form the initial framework for the design.
4. Perform Thermal Design:
The thermal design phase requires complex calculations to determine heat transfer rates, temperature profiles, and overall performance. A deep understanding of heat transfer principles and material properties is essential to optimize heat exchange while meeting operational goals.
5. Perform Mechanical Design:
Mechanical engineers ensure the heat exchanger can withstand the mechanical stresses and pressures it will encounter during operation. This includes selecting appropriate materials, determining wall thickness, and ensuring structural integrity.
6. Cost Analysis:
Balancing performance with cost is crucial. A thorough cost analysis helps identify opportunities for cost savings without compromising performance.
7. Safety and Codes:
Adhering to safety standards and regulatory codes is paramount. Compliance ensures the heat exchanger operates safely and within legal requirements. This step may involve pressure vessel codes, material specifications, and safety protocols.
8. Prototype and Testing (if applicable):
Creating a prototype and conducting testing, when feasible, can validate the design and identify any potential issues before full-scale production. This step is particularly important for novel or high-risk designs.
9. Documentation and Drawings:
Accurate documentation and detailed engineering drawings are essential for manufacturing and installation. This step ensures that the design specifications are accurately translated into the final product.
10. Fabrication and Installation:
Fabrication involves constructing the heat exchanger according to the design specifications. Attention to detail during this phase is vital to ensure the final product meets the intended performance and safety requirements. Installation should follow best practices for proper functioning.
11. Maintenance and Monitoring:
After installation, ongoing maintenance and monitoring are crucial to ensure the heat exchanger continues to operate efficiently and safely. Regular inspections, cleaning, and upkeep are essential to extend the equipment’s lifespan.
Conclusion:
Optimizing the thermal design of a shell and tube heat exchanger is a multifaceted endeavor, demanding expertise in heat transfer principles, material science, and engineering standards. Engaging experienced mechanical and thermal design engineers is often advisable to navigate this process successfully. By following these well-defined steps, you can ensure your heat exchanger meets its performance goals while minimizing costs and complying with safety and regulatory requirements.
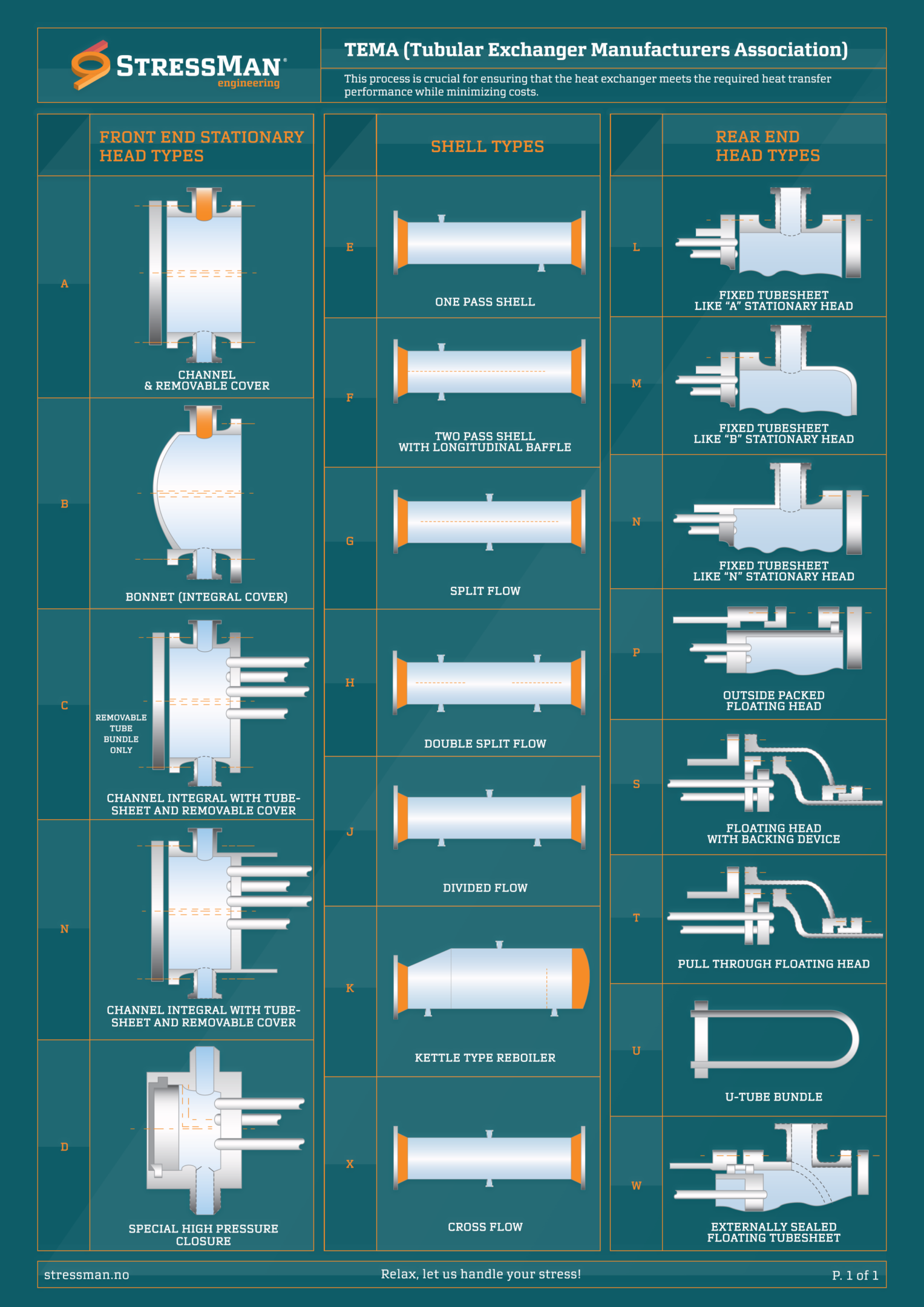
Download the hi-res PDF here