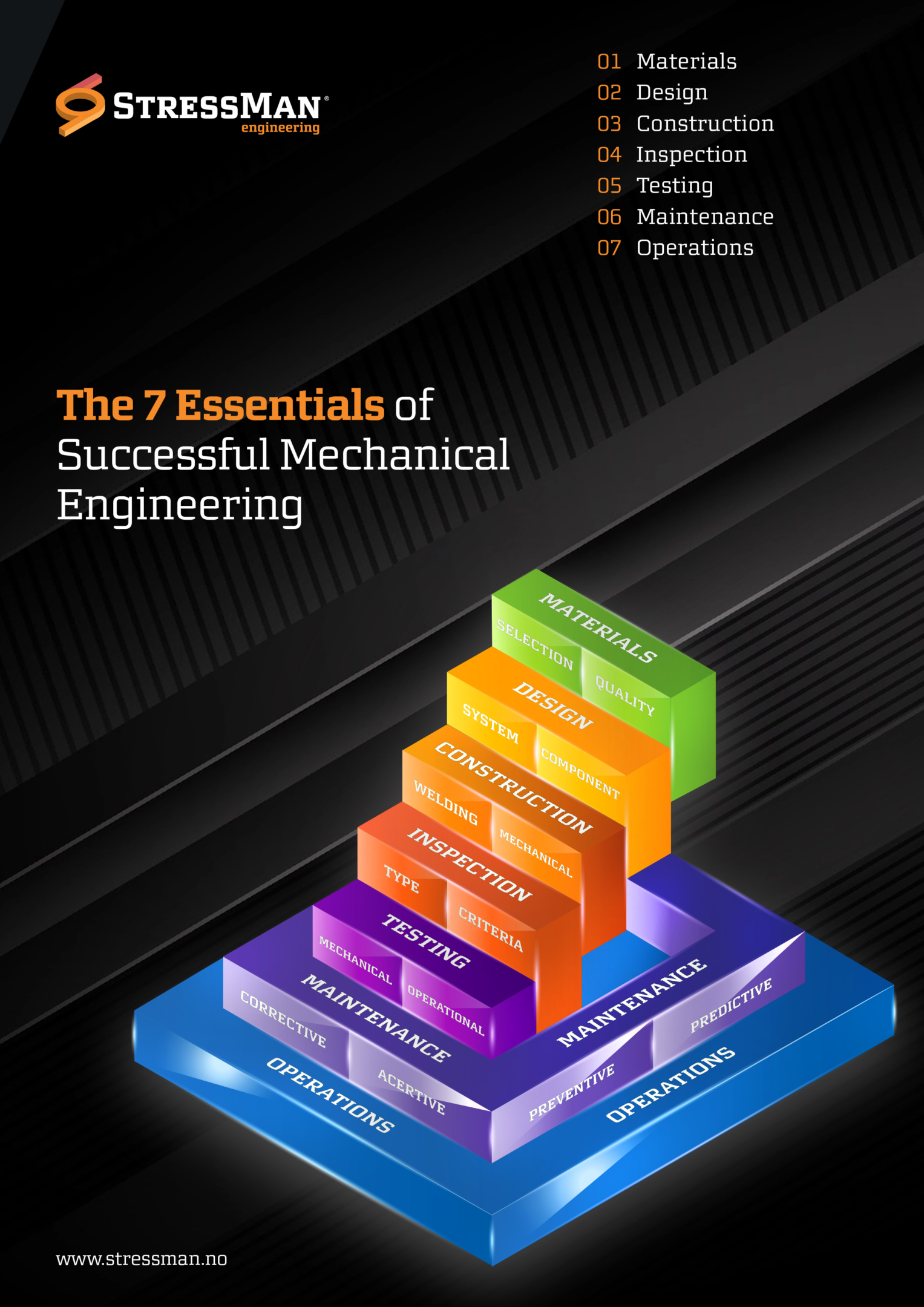
In each of the seven fundamental areas, the responsible engineer must make a series of decisions to achieve the optimum and most cost-effective operation. The following checklists summarize the key decision points related to piping and pipeline activities:
01 Materials
02 Design
03 Construction
04 Inspection
05 Testing
06 Maintenance
07 Operation
01 Materials
Choice of material specifications.
Code listed or unlisted materials.
Consistency of material form with code.
Compatibility of materials with fluid and temperature range.
Compatibility of materials with each other.
Minimum temperature and toughness.
Maximum temperature and strength.
Weldability, welding electrodes.
Supplementary requirements (carbon equivalent, corrosion testing, etc.).
Lining, coating, paint, cathodic protection, galvanizing.
Need for material test reports, positive material identification, and traceability.
Oversight and hold points.
Proper repairs to materials, and post-repair inspections.
Experience with similar materials and services.
Degradation mechanisms and service life. Corrosion allowance.
Design limitations (flow, temperature, trace elements, cleaning, etc.).
Material records, filing, and retrieval logic.
02 Design
02.1 System Design
System Function:
The technology of the process: fundamentals, experience, and development.
Process cost-benefit.
Operating and safety logic and viability.
Process and instrumentation diagrams (P&ID).
System descriptions.
Redundancies and separation.
Layout drawings.
Interfaces with other systems.
Pressures, temperatures, and flow rates (throughput).
Heat transfer and heat loss.
Design life, future throughput.
Sizing pumps, valves, compressors, blowers.
Power supplies.
Air, water, utility supplies.
Normal operation.
Credible accident conditions.
Overpressure protection (relief valves, rupture disks, interlocks, etc.).
Safety and environmental analyses.
Operating envelope and technical specifications.
System design records filing and retrieval logic.
02.2 Component Design:
Codes and Standards:
Regulatory and contractual requirements.
Design Specifications (input) and Design Reports (output).
Equipment interfaces and code boundaries.
Layout logic and critical dimensions.
Hazard classification (lethal, safety class, etc.).
Design maximum and minimum pressures (vacuum, internal or external pressure).
Design maximum and minimum temperatures.
Normal operating loads (weight, pressure, temperature, valve thrust, lifting, etc.).
Local and contact-bearing stresses.
Fatigue loads and cycles.
Extreme loads (wind, seismic, explosion, water-hammer, etc.).
Extreme loads qualification.
Load combinations.
Corrosion allowance.
Strength and stability design.
Fracture prevention and toughness design.
Design of openings and reinforcements.
Overpressure protection.
Equipment nozzle loads.
Component load-displacement limits (mechanical fittings, expansion joints, etc.).
Unlisted components (rating of non-B16 fittings, proof testing, etc.).
Design of support structures and attachments.
Provisions for maintenance access.
Experience with similar designs and services.
Piping specifications.
Equipment specifications (pumps, valves, compressors, tanks, vessels, etc.).
Mechanical flow sheets with piping and equipment specifications.
Detailed design drawings, isometrics, and orthographics.
Design quality assurance: software, calculations, drawings, and specifications.
Professional Engineer certifications.
Mechanical design records filing and retrieval logic.
03 Construction
Procurement and “make or buy” decisions.
Fabrication and procurement specifications.
Bid criteria and suppliers selection.
Fabricator experience, schedule, warranties, compensation.
Drawings, critical dimensions, and tolerances.
Planning sequence: procurement, shop fabrication, and field erection.
Personnel, craft experience, training, proficiency.
Personnel and process certifications.
Welding procedures.
Procedures for bending, flange joining, and threading.
Procedure for mechanical joining, compression fittings, and assembly.
Pre-heat and post-weld heat treatment.
Leak testing (hydro, pneumatic, sensitive leak, etc.).
Control and disposition of non-conformances.
Permitted repairs of fabrication flaws.
Construction records filing and retrieval logic.
Hold points and inspection interfaces.
As-built reconciliation of design.
04 Quality Control Inspections
Examinations (quality control) and inspections (quality assurance).
Examination methods and percentages.
Personnel and process certifications.
Calibration of examination tools.
Surface or volumetric examinations.
Acceptance criteria.
Hold points and independent inspections by owner representative.
Control and disposition of non-conformances.
Documentation of inspections.
Inspection records filing and retrieval logic.
05 Preoperational Testing
05.1 Mechanical Testing
Leak testing technique (hydro, pneumatic, sensitive leak, etc.).
Test boundaries.
Test fluid and pressure.
Testing cautions.
Test personnel.
Hold points.
Start-up testing.
Vibration startup monitoring.
Thermal expansion startup monitoring for hotlines.
Test acceptance criteria.
Control and disposition of non-conformances.
Mechanical test records filing and retrieval logic.
05.2 Operational Testing
Component operability tests.
System flow tests.
Instrumentation and controls tests.
Commissioning.
Measurements of key process variables and acceptance criteria.
The turnover process from engineering and maintenance to operations.
Operational test records filing and retrieval logic.
06 Maintenance
Corrective: run-to-failure
Preventive: adjust or replace at fixed intervals.
Predictive: inspect and decide based on fitness-for-service analysis.
Active vs. reactive (corrective, run-to-failure) by system and by component.
Active: planned (fixed interval) vs. predictive (trended) maintenance.
Analysis and trending of maintenance history.
Reliability analysis.
Maintenance feedback and lessons learned process.
On-stream (in-service) or outage (shutdown) maintenance.
Sampling and corrosion monitoring.
Visual (external or internal, direct or remote).
Surface (liquid penetrant, magnetic particles, etc.).
Volumetric (radiography, ultrasonic, etc.)
Periodic hydro test.
Fitness-for-service (run-or-repair) analysis: API-579, ASME XI, B31.G, etc.
Qualified welding or mechanical repairs
Corrosion repairs, lining, and coating.
National Board certification of the repair program.
Repair stamp (R, VR).
End of system or component life
Shutdown and disposition plan.
Maintenance records filing (electronic database) and retrieval logic.
07 Operation
Operator experience, proficiency, and certification.
Operating procedures.
Operating envelopes and limits.
Emergency procedures.
Understanding operating processes, and access to system engineers.
Role of shift engineer.
Alarms, facility drills, and emergency response.
Standing orders and shift orders.
Shift turnover process.
Authorities to operate the equipment.
System descriptions and up-to-date system diagrams.
Equipment labels.
Normal operating loads in service: weight, temperature, pressure, flow.
Accident loads: large vibration, water-hammer, winds, seismic, explosion.
Log and analysis of operating and accident conditions.
Understanding degradation in service and abnormal response.
Analysis of abnormal events.
Lessons learned, plant, company, and industry feedback.
Engineering reviews and hold points.
Post-maintenance turnover.
Operating records filing and retrieval logic.
Audits, critiques, self-assessment, and continuous improvement.
Prioritization process for upgrades and projects.
Interface operations-maintenance-engineering.
Temporary modification process.
Change control process.
Production objectives, measurement, trending, and improvement.